Project Production Institute 2017 Symposium:
Managing The Global Supply Network
“Imagine you own every part of your supply chain, how would your decisions in managing it differ?”
– Professor Philip Kaminsky, Department of Industrial Engineering & Operations Research, University of California at Berkeley
The fourth annual Project Production Institute Symposium was held on 29 November 2017 in San Francisco. Once again, the Symposium drew record attendance from representatives across multiple industries and academia from around the globe to hear the latest in managing complex supply networks to address the crisis in global engineering and construction.
Executives from a wide variety of companies such as Applied Materials, Chevron, Devon Energy, Facebook, Roche, Genentech, Google, Hess, Intel, McKinsey & Company, Merck, Microsoft and S&P Global came together with researchers and academics from Santa Clara University, Stanford, UC Berkeley and UCLA to discuss how to resolve the global crisis affecting the construction and engineering industry through effective application of Project Production Management (PPM).
In pursuit of its mission to address this global crisis, the Institute focused its efforts over the past year on growing its membership both in number and to include more sectors and industries. As a result, individual memberships grew 3 fold to more than 1000 members representing the wide range of industries who depend upon engineering and construction. In addition, through its program to disseminate information on the application of PPM via technical journals and seminars, the breadth of industries interested in the application of PPM to their capital projects greatly expanded. To kick off the day, Kerry Haley, Project Production Institute’s (PPI) Executive Director introduced the topic for the day, around which the entire Symposium agenda was organized – Managing the Global Supply Network. She described the Institute’s funding of research at the University of California Berkeley to investigate supply chain dynamics in large capital projects in the oil & gas industry, using the topic to introduce the Symposium’s plenary speaker, Philip Kaminsky, Professor in the University of California Berkeley’s Department of Industrial Engineering and Operations Research, and Executive Associate Dean for Student Affairs in the College of Engineering.
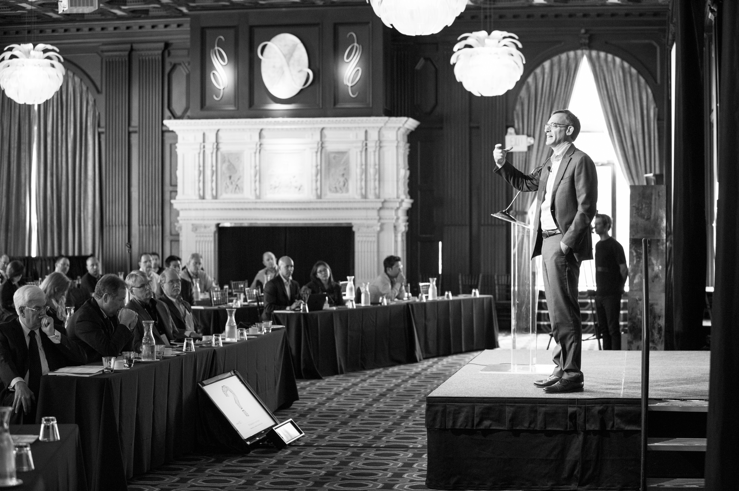
Professor Philip Kaminsky, UC Berkeley and member of the PPI Technical Committee
Professor Kaminsky’s talk framed the Symposium agenda for the day. He described initial findings from research conducted by UC Berkeley graduate student Arman Jabbari and himself, which were the result of interviews conducted with a number of personnel working in the oil & gas sector. He began by noting that project execution performance in large capital projects in the oil & gas industry was typical of performance across all industries. Specifically, that most large oil & gas projects incurred very large cost overruns (typically greater than 30% of initial budget) and/or were very late (typically greater than 40% later than the target schedule). This simple observation motivated the question he posed to the audience: “Is there a problem with capital project supply chain management?” whereby he observed that a symptom would be the presence of too much inventory arriving too soon on a construction site.
From that initial observation, Kaminsky outlined a number of questions posed by his student to those interviewed. They asked what the participants understood by the term “supply chain management”; what their view of the industry’s performance in managing supply chains was; how suppliers worked and coordinated with their customers; how customers worked with suppliers to assure delivery dates; the types of tools used to plan and manage supply chain activities, and their reliability and effectiveness.
Kaminsky outlined the responses and wove in observations and suggestions from the “state of the art” in supply chain practices used in a variety of industries. Interview participants sometimes confused procurement with what is currently understood to be “supply chain management”. Most participants believed that the current performance of the oil & gas industry was close to optimal. Participants seemed to underestimate the cost of holding inventory, while overestimating the costs of avoiding schedule delays through early deliveries of as many construction materials as possible as a pre-emptive measure. They were skeptical about the practical application of “just-in-time” methods, or more sophisticated modeling of supply flows to manage and coordinate deliveries. Among the tools used were standard project planning and scheduling techniques typically using well-known software such as Microsoft Project, Excel, or Oracle Primavera. Kaminsky also remarked on the pervasive theme of organizational silos between suppliers and customers, and within customer organizations, as well as misaligned incentives that characterized the comments of many participants.
From this current state of play in oil & gas capital projects, Professor Kaminsky then highlighted some useful directions for the audience. He described a more holistic view of supply chain management as a set of approaches to efficiently integrate suppliers, manufacturers, warehouses and stores so that merchandise and supplies are produced and distributed in the right quantities, to the right locations at the right times, in order to minimize system-wide costs while satisfying service level requirements. After introducing the notion of efficient frontiers to the audience to assess how effectively a supply chain might perform, he hypothesized the current state in oil & gas supply chains was the result of local greedy optimization rather than global optimization. He concluded by describing a program of research to evaluate some of the hypotheses he articulated, by gathering data to develop simple quantitative models for sample supply chains in oil & gas capital projects. His overall presentation summarized a number of the outstanding issues in capital project execution for the audience. Subsequent talks on the day proceeded to elaborate on a number of those aspects.
Matthew Parsons, Partner at McKinsey & Company, leading McKinsey’s Americas Capital Projects & Infrastructure Practice, then followed with a presentation describing additional implications to capital projects of less than effective supply chain management. He categorized consequences in terms of their impact on the business, design and execution elements of projects. Among the most severe business consequence was the need to make capital and other resource commitments far earlier than needed because of inordinate lead times and other contingencies that required fixing project scope and requirements earlier than needed. For project design, the consequences were design inflexibility and higher costs of change from the loss of ability to make decisions in natural cadence with the development of a project. Another consequence was the unanticipated work and cost associated with poorly thought out modularization decisions whereby the longer lead times necessitated by off-site fabrication frequently added unintended delays and costs. Finally, he described how project execution suffered in a variety of ways including rework, and the associated work and costs of holding inventory longer than planned and managing for obsolescence and theft. Parsons concluded with a quick history of advances in the thinking and implementation of supply chain practices and a call to action to train a new generation of capital project leaders rather than capital project administrators.
Ram Shenoy, PPI’s Technical Director, resumed the agenda presenting a recently articulated position of the Institute comparing Project Production Management with Lean Manufacturing and Lean Construction. He first alluded to the history of Lean and Lean Construction, referencing early literature from the 1980s and 1990s in peer-reviewed academic operations science literature whereby leading researchers in the area had put a sound theoretical basis to the general body of principles that today comprise Lean. A concrete example of those research contributions was a clear and consistent definition of push and pull systems, a view of all lean principles – muda, mura, muri – as essentially different ways of minimizing the costs of variability, and the introduction of CONWIP (Constant Work In Process) as a hybrid push-pull system of production control that could, in certain circumstances, surpass push or pull in performance. Shenoy concluded with an observation that the emphasis of Lean Construction in recent years has moved away from its operations sciences roots and moved toward ways of managing human interactions/interfaces between different stakeholders in project delivery.
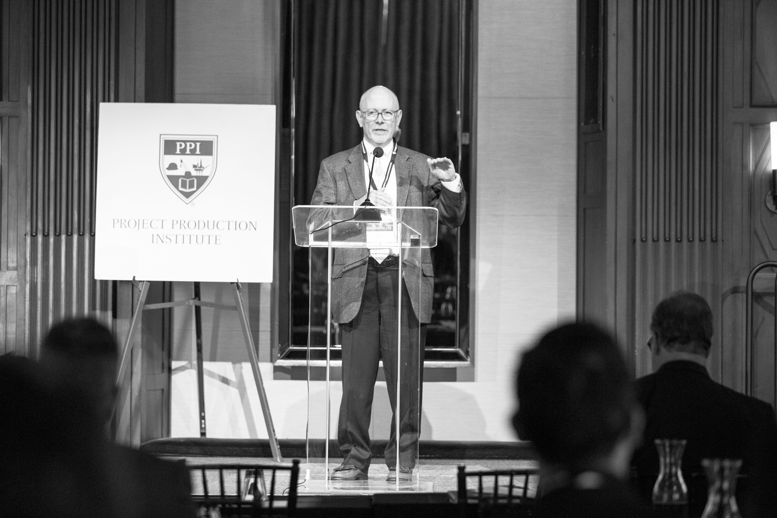
David McKay, Hess Corp and PPI Advisory Board Member, introduces H. James Choo
To close out the morning session, H. James Choo, Chief Technical Officer of Strategic Project Solutions Inc., gave a talk about the potential for lead-time compression to improve capital project performance. Choo started with a classic graphic adapted from the Harvard Business Review showing that the very presence of WIP reduces the ability to influence the trajectory of project execution by extending the time for completion of a project. He then proceeded to give elementary definitions of lead-time, cycle time and process time, distinguishing between the three, and showing how the indiscriminate addition of contingencies can significantly increase cycle time and lead-time over process times. Choo then showed three distinct types of supply flows that are encountered in most capital projects resulting from whether components are made-to-stock, made-to-order or engineered-to-order. With a simple example he showed how different types of control signals to release work can reduce WIP (and cash consumed), allow greater time for making decisions and allow greater flexibility. The advantage of thinking carefully about policies for controlling and releasing work to enhance overall project performance, as Choo concluded, is the ability to finish the project faster (faster time to market) or the ability to defer a start, to allow greater time for decisions to be made and for uncertainties to be resolved.
Following lunch, a keynote was delivered by Marc Tarpenning, one of the two co-founders of Tesla Motors. Tarpenning gave a unique and insightful perspective into how two Silicon Valley entrepreneurs started an electric car manufacturer, motivated initially by seeking solutions to a big problem – notably addressing climate change. He described how they were inspired to look for ways to reduce uses of oil, which led to developing alternative modes of transportation not powered by oil. He rapidly went through the reasoning behind developing high-density electric batteries and how Tesla arrived at its first market niche of fast light sports cars, by looking at how other electric car manufacturers had singularly failed to produce products that consumers would wish to buy. He concluded by outlining an optimistic future for growth in the use of electric vehicles and for Tesla.
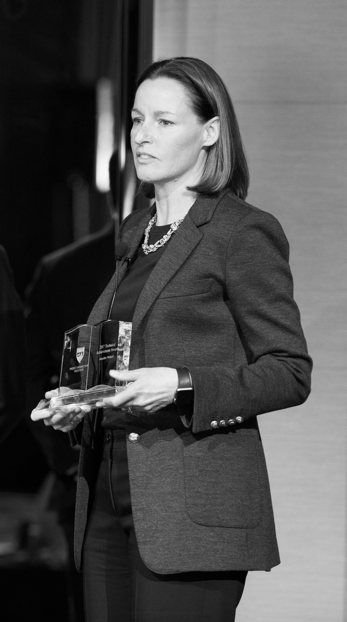
Jennifer Weitzel, Microsoft Corp., Recipient, 2017 PPI Technical Achievement Award
The Institute presented its 2017 Technical Achievement Award to Jennifer Weitzel, General Manager of the Global Data Center Program at Microsoft Corp. The Institute made the award to Weitzel in recognition of her long career and experience as a practitioner applying PPM across a variety of industries ranging from civil infrastructure, retail operations and technology, and in capital projects of increasing size and complexity, culminating in her current leadership role in Microsoft Corp. Since the award was made, Weitzel has since expanded her responsibilities to include global engineering and construction for the company. She is also a member of the Institute’s Industry Council.
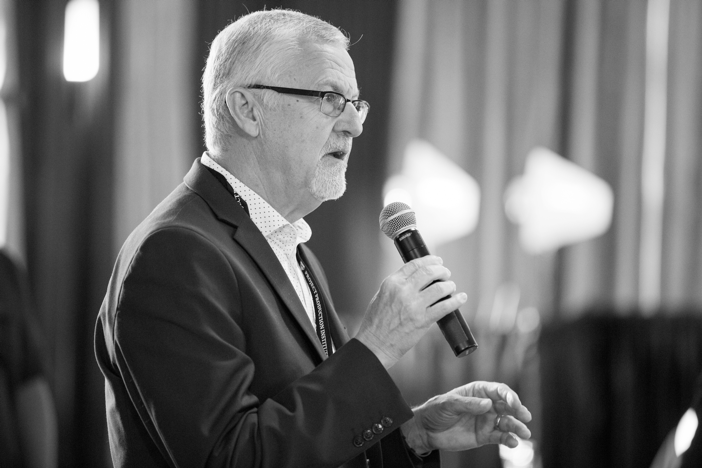
Wayne Crabtree, Chevron Corporation and PPI Industry Council Member
A presentation by Wayne Crabtree, Continuous Improvement Advisor for the Chevron Project Management System (CPMS) at Chevron Project Resources Corporation and a member of the Institute’s Industry Council began the afternoon program. He addressed the impact of supply chains on major capital projects, citing examples from Chevron. Among the potential consequences of poor supply chain management, Crabtree cited less control of time to market, having to make decisions earlier than necessary to commit to technology prematurely, and additional costs of holding and handling inventory as being particularly significant. He illustrated these points to spectacular effect with examples from Chevron’s Gorgon project describing escalating costs of astonishing magnitude, due to the size and scale of the project. He concluded by describing elements of Chevron’s adoption of PPM, talking about the introduction of decoupling inventory buffers into the supply flows, mapping and understanding the sources of variability in the global supply flow network, mapping the detailed production system and the introduction of a CONWIP strategy in the short-term supply flow planning process.
By way of introduction for the next speaker, Dr. David Bray*, a member of the Institute’s Technical Committee, shared the following haiku he created to summarize the key messages on the day:
Variability
Production in the face of more Complexity
Questions of Scale, Scope
In a Changing, Networked World
Exponential Times
Make Flows Visible, Rethink Risky Processes, Cap and Control WIP
Design End to End
Synchronized Execution – Pull Signal, Control
Deliver Results
Differently, Better and Lead the Change Our World Needs
*Used with permission
Matt Holzemer, program manager on Google’s Data Center team went on to describe myriad supply challenges encountered in construction projects over the course of his career. He cited examples from a number of construction settings: an airport terminal; a hospital, a museum and data centers. He contrasted supply flows in a capital project with supply flows in other settings, for instance, in retail and in manufacturing. He pointed out that supply flows in capital projects are subject to huge and numerous sources of variability, presenting the need for projects to match multiple asynchronous supply flows converging at the point of construction. He noted the increasing complexity of projects, which are subject to dynamic uncertainty, rendering production forecasts inaccurate more often than not. He commented on the need to shorten lead times to manage project uncertainties, for instance for technology selection, concluding that a system view of a project should naturally account for an appropriately agile and adaptable supply chain for a project.
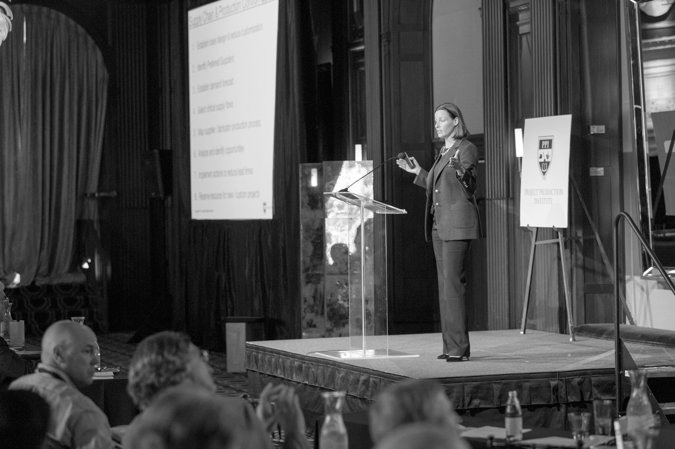
Jennifer Weitzel, Microsoft Corporation, PPI Industry Council Member
Jennifer Weitzel, General Manager of Microsoft’s Global Data Center Program, then discussed select challenges in optimizing the supply flows in the Microsoft global data center program. She started by describing the business drivers for growth in data center construction across the entire industry of cloud service providers and data center owners. A consequence of this growth is that the available capacity of labor and skills available in certain geographic regions to support the construction of data centers is less than demand. As such, Weitzel outlined some steps Microsoft has taken to manage those challenges in terms of reducing customization in its base designs, identifying, qualifying and securing preferred supplier capacity, establishing its demand forecast and actively tracking critical supply flows. She illustrated some of these steps, showing a sample equipment supply network and outlined moves away from single sourced custom equipment toward multiple sourced, standardized designs. She concluded by showing some early results achieved on lead-time reductions and improvements in overall cycle times.
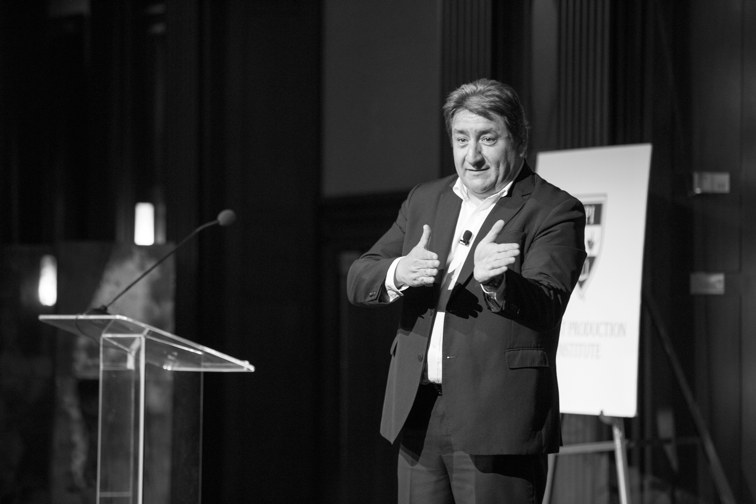
Roberto Arbulu, Strategic Project Solutions, Inc.
Roberto Arbulu, VP Operations for Strategic Project Solutions Inc., gave the final talk of the day using a case example on effective supply flow control. Arbulu started by showing some conclusions from a 2015 PPI technical research report co-authored by Professors Iris Tommelein and Glenn Ballard of the University of California at Berkeley in which they hypothesized some potential consequences of deploying Advanced Work Packaging (AWP) in construction projects. They anticipated inventory growth; longer project durations and higher labor costs without the requisite care being taken in the implementation of AWP. He went on to describe a large capital project in which all the hypotheses of Tommelein and Ballard were shown to be true. In describing the supply flow and its relationship to the construction point of installation, he explained that there was a severe mismatch between the demand for materials at the point of installation and the rate at which supplies could be made. This misalignment between supply and demand resulted from a combination of factors – use of workface planning (WFP), shared transportation logistics capacity, and conventional project controls used to schedule demand, they completely mismatched the size and number of the work packages. The result was the loud refrain from the worksite “We cannot get what we need when we need it”. He showed that the mismatch of supply and demand was the result of variability that led to excessive WIP leading to the cost and schedule overruns predicted by Tommelein and Ballard. He concluded by showing how to address the problem from a production systems perspective, namely, taking steps to increase the reliability of demand; pull materials to the point of installation; and control and continually optimize supply. He showed the modified supply flow, and the resulting improvement in performance metrics such as demand reliability, system throughput and cycle times.
The Symposium concluded with Kerry Haley and Ram Shenoy presenting a synopsis of key messages from the presentations of the day. They described the Institutes calendar of events for 2018 and reminded the audience of the different Institute resources available from the PPI website, such as the glossary and technical journals.
Their final message: Get the word out to your teams to join the Institute and join them for the 2018 Symposium set for 05-06 December 2018 at the Four Seasons in San Francisco.